Your Die & Mould Experts!
Glider Guard Tool & Die is a full service die and mould tooling shop recognized as an industry leader in decorative and surface trim tooling. Our assembly fixtures are second to none and our prototyping and tryout facilities are great assets to any concept/design phase. We operate with a full complement of CNC machines, wire and sinker EDMs, using the latest in CAD/CAM technology.
Glider Guard has designed and built a number of high performance tools including stamping dies, progressive dies, injection moulds for plastics and multi-action moulds for major auto manufacturers and their Tier 1 and Tier 2 suppliers.
As well, we have contributed considerable experience and ingenuity on the revolutionary method of joining diverse materials in a single stamping/moulding process known as Insert-Moulding. These products continue to be a growing part of the decorative and trim tooling market.
“NECESSITY IS THE MOTHER OF INVENTION”
The origins of the Glider Guard name go back as far as the 1940’s when our company’s founder invented a stamped metal part to guard the blades of tractors that tilled the corn fields surrounding Windsor. The part was ingenious because it protected the blade from damage while allowing for full functionality. The part was called the Glider Guard, and thus the company’s name and reputation were born.
At Glider Guard, we like to think it’s the spirit of ingenuity – the transition from the need for specifically designed, high quality parts to the inventive processes that fulfill those needs – that sets us apart from our competition.
History
Glider Guard was founded in 1945 as a tool & die and part production facility. When the Cox family took control of the company in 1980, its focus was shifted to tooling. Increasing demand for Glider Guard services, technology upgrades and heightened production values industry-wide permitted the addition of CAD/CAM and CNC capabilities in 1988. Within two years, the company had outgrown its original home and moved to a new facility in Oldcastle.
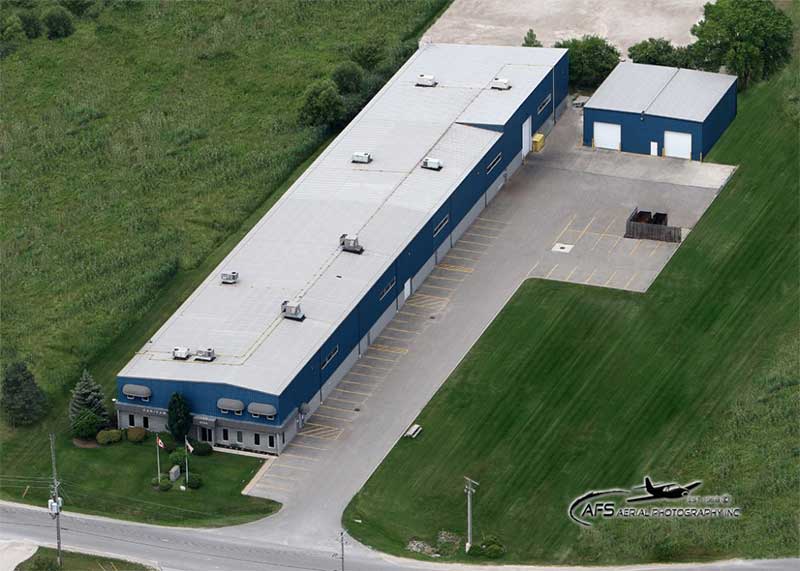
Glider Guard – Plant 1
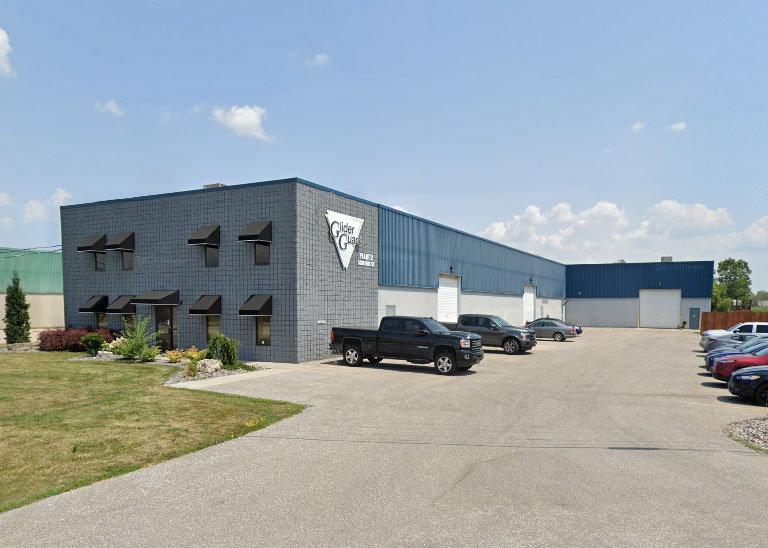
Glider Guard – Plant 2
Our manufacturing capabilities have also progressed through the acquisition of various presses (try-out and spotting), CNC machining centres (horizontal and vertical), EDM machines (sinker and wire) and a host of other cutting-edge shop essentials.
Recently, Glider Guard has invested heavily in modern, state of the art equipment. Utilizing an array of high speed CNC machining centres allows us to produce tooling quicker and more accurately than ever before. In our EDM department, the acquisition of a two new Makino wire EDMs has more than doubled our capacity. Our tool room equipment has not been ignored either. Two new large capacity saws give us the flexibility to utilize almost any block of steel. New acquisitions in our milling, turning and grinding departments have also kept pace with advancing technologies.
Our tryout facilities have evolved as well. Our fully automated feed line allows us to try-out blank and progressive dies in a full production environment. With multiple large capacity press cells ranging from 200 to 400 tons, we have the flexibility to tryout many tools at the same time.
To keep up with the growing demand for our services, Glider Guard runs two full shifts.